We follow strict quality assurance procedures, under ISO 9001 and ISO 13485 certification, and devote significant resources to quality control throughout the production process in order to meet your requirements
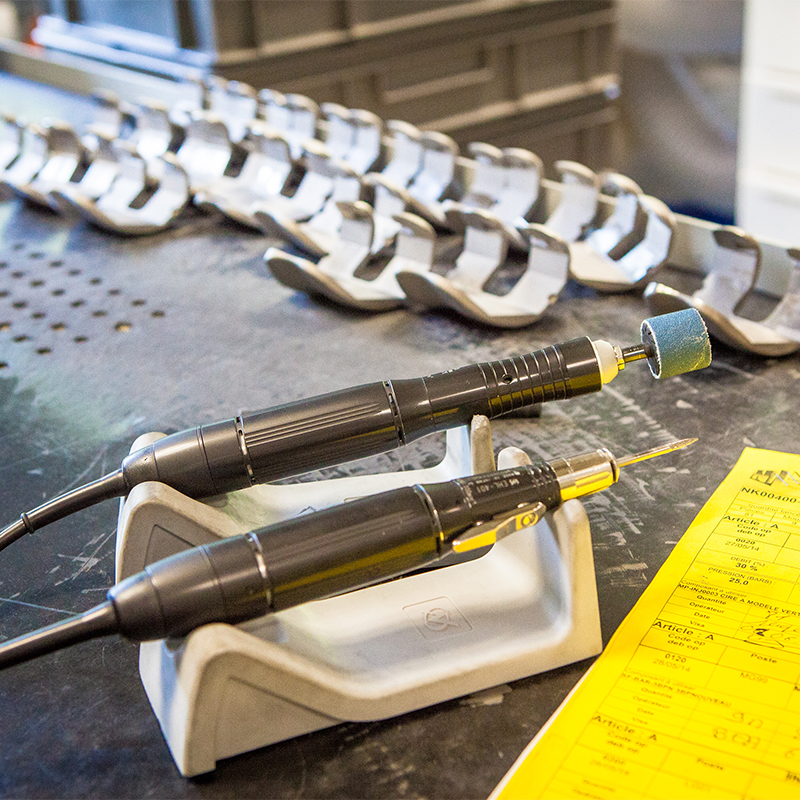
Guaranteed traceability at every stage
We ensure part quality and traceability through a production order (PO) that identifies each batch and stays with it through to the final quality check. The PO contains all the manufacturing stages, the associated parameters and the relevant documentation. All the production controls are listed in it.
A quality control file is established at the client’s request and provided with the parts on delivery. The file includes all the conformity certificates and quality control reports specified in the PO.
The PO, along with the quality control file and all the records relating to the batch are archived for a period of 10 years for industrial parts and 35 years for medical part batches.
Our standard tests
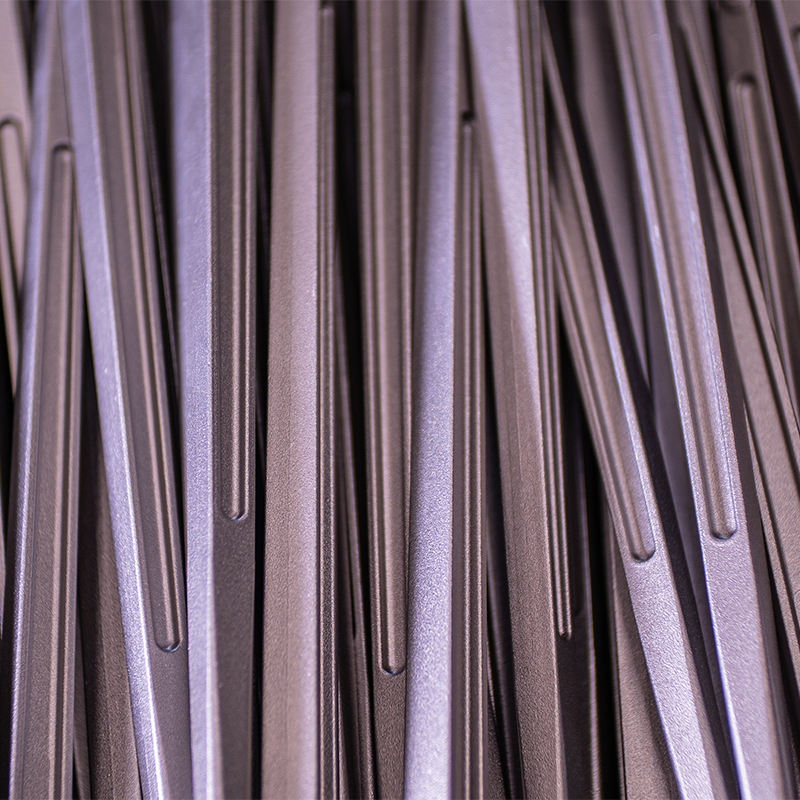
Chemical composition test
Each raw material batch is checked by spectrophotometric analysis on reception to ensure conformity with the supplier’s material certification.
The chemical composition is checked in our laboratory for each cluster that is cast. If requested by our clients, the results are entered in the material certifications (according to NF EN 10204) enclosed with the parts on delivery.
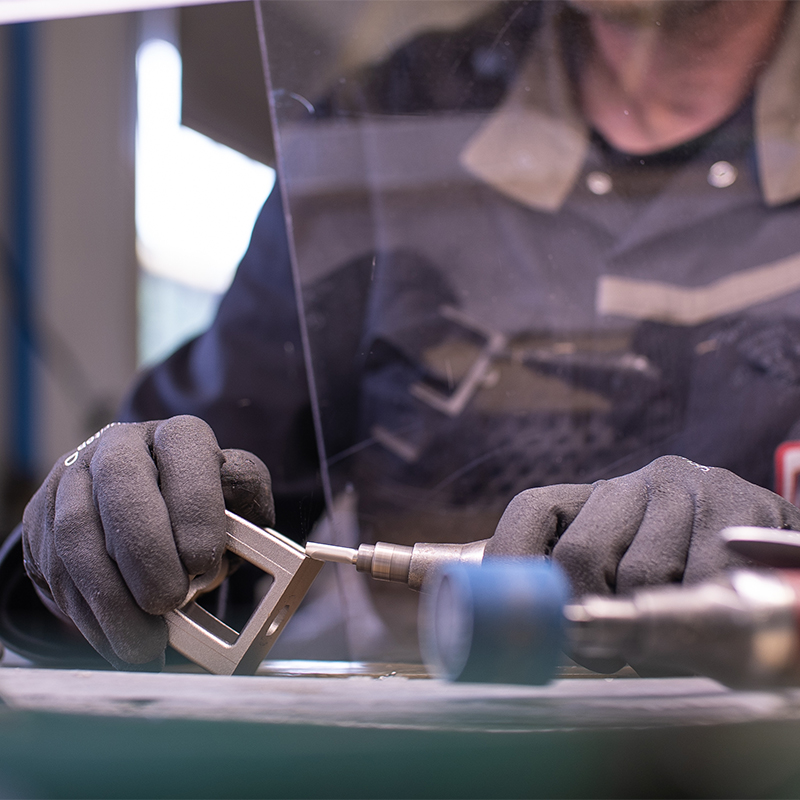
Visual tests
A visual inspection of each cast part is carried out with the naked eye or using a magnifying glass, to check the shape, dimensions and external and internal surface aspect.
The acceptance criteria are defined according to our clients’ specifications and allow us to deliver parts with 100% conformity.
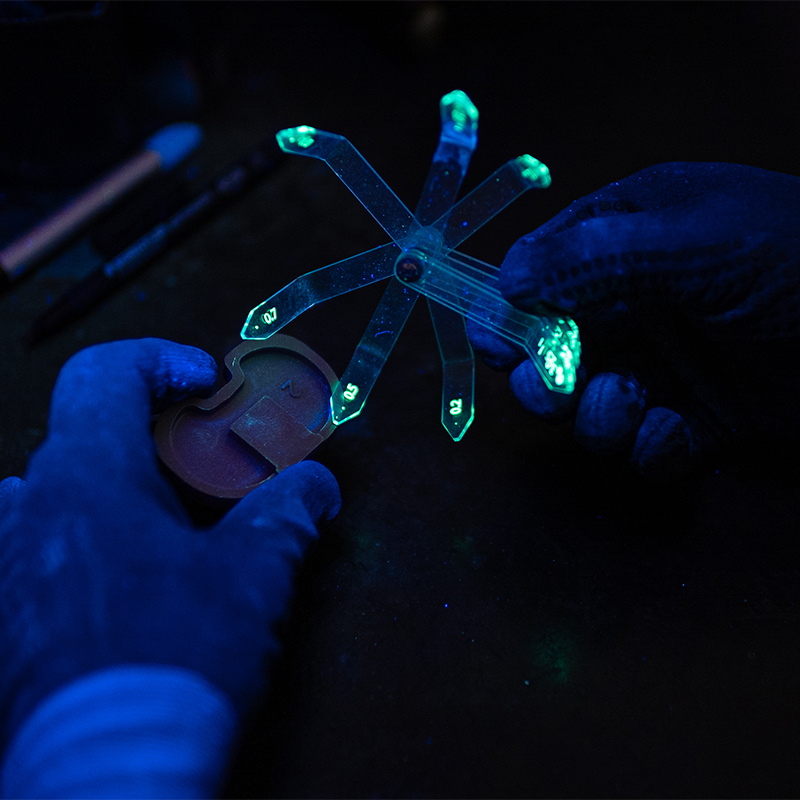
Non-destructive tests
Non-destructive tests include penetrant testing or radiography. They are not systematic and are carried out according to your needs.
Internal penetrant tests are carried out by a COFREND certified technician. Radiography is carried out by an audited and certified service provider.
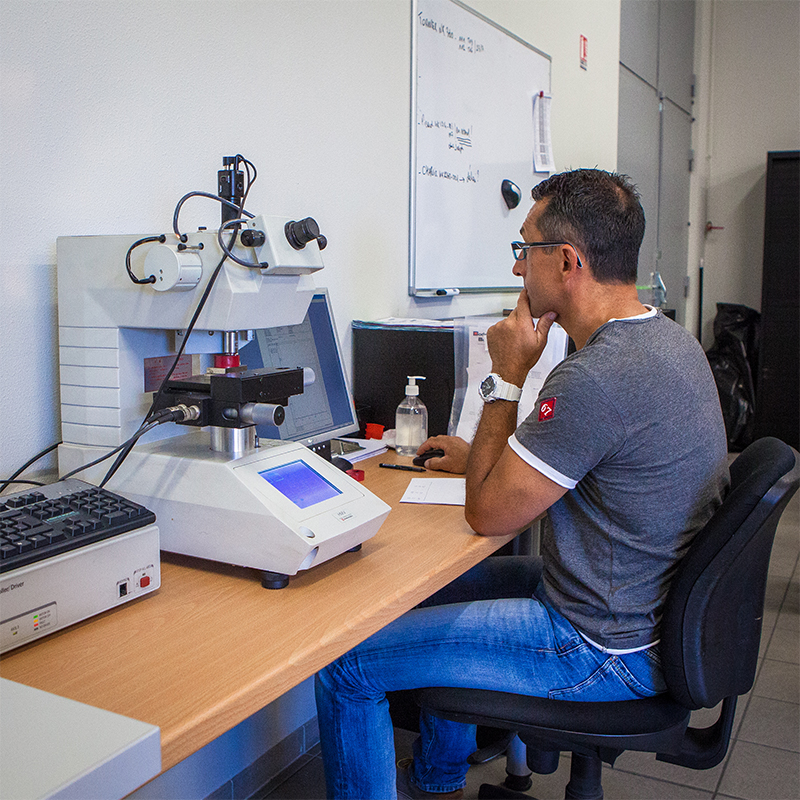
Mechanical characteristics test
The mechanical tests are carried out after thermal treatment on special test samples (treated at the same time as the parts), at the client’s request. They show whether the parts comply with the specifications defined in the applicable standards.
Tension and compression tests are carried out in our in-house laboratory. Metallographic tests (on grain size, oxide levels, etc.) can also be performed on request.
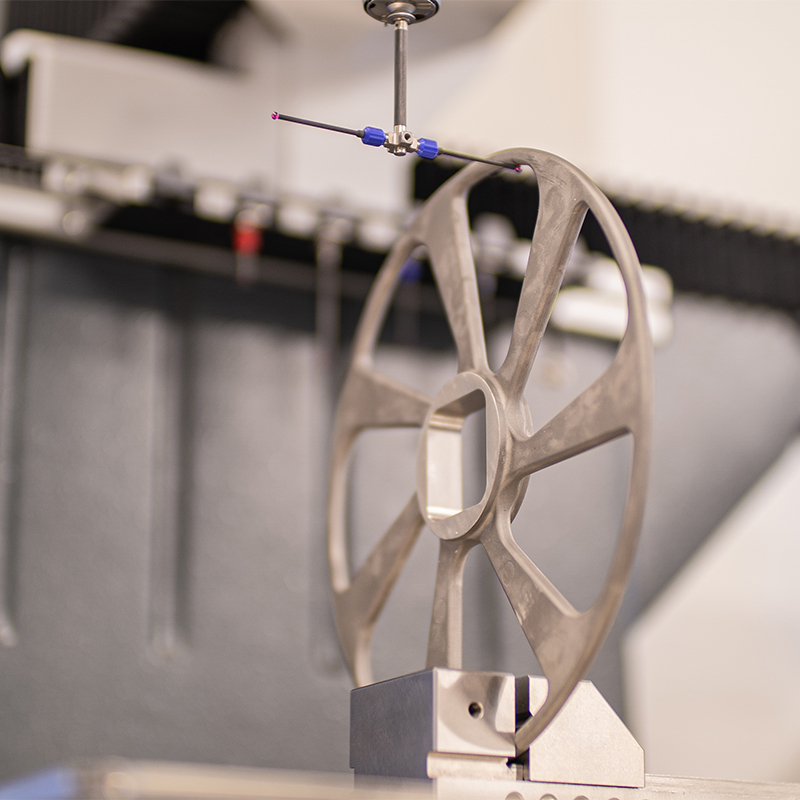
Dimensional tests
Our metrology laboratory is equipped with all the equipment required to perform dimensional tests in the development phase or during production runs:
- Scan 3D measuring equipment,
- Tri-dimensional measurement machine,
- 3D measuring arm,
- Measuring column,
- Profile projector,
- Conventional tools: calipers, micrometers, etc.